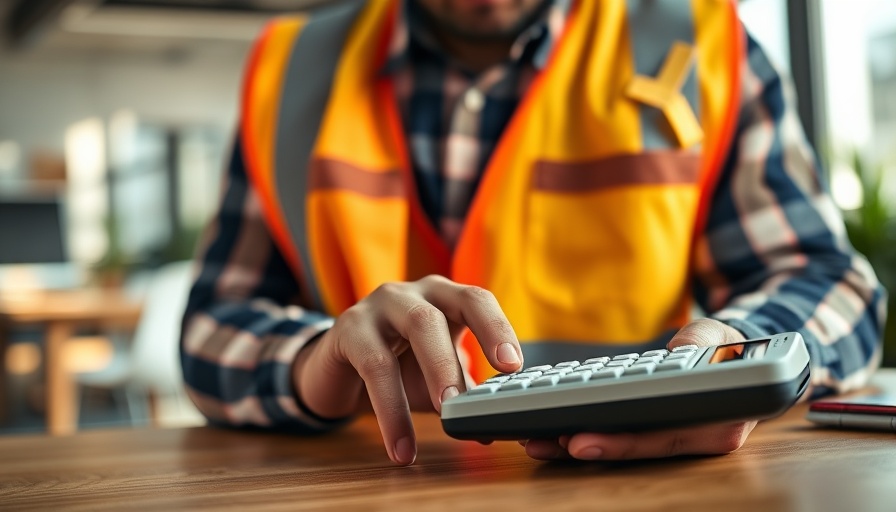
The Impact of Trump's Tariffs on Facility Management
In the murky waters of U.S. trade policy, facility managers find themselves navigating a continually changing landscape due to upcoming tariffs under the current administration. While Donald Trump's administration is susceptible to unpredictability regarding trade announcements, the implications for facility management remain clear: costs and project timelines may escalate significantly.
Understanding Tariff Sensitive Categories
Recent analyses highlight specific product categories that are particularly susceptible to increased tariffs. These categories often represent significant import values and, subsequently, cost structures for facility managers. Major categories that may face price hikes include:
- Iron and Steel
- Nonferrous Metals
- Construction Machinery
- Major Appliances
- Furniture
Each of these components plays an essential role in construction and facility management, meaning any changes in their costs could directly impact budgets and timelines.
Project Timelines and Supply Chain Challenges
In addition to direct costs, the tariffs may also lengthen project timelines. Given that many materials rely heavily on international sourcing, delays in supply chains could emerge. For instance, tariffs on construction machinery not only increase costs but can also result in back-ordered supplies. This increased wait can stymie the pace of projects, forcing facility managers to rethink scheduling and allocate resources accordingly.
Opportunities in a Challenging Environment
However, amidst challenges come opportunities. Facility managers may re-evaluate vendor contracts or increasingly seek local suppliers to mitigate impending price increases. Building relationships with domestic manufacturers could not only lead to cost savings but also more reliable timelines, as local suppliers might be less impacted by international tariffs.
Navigating Uncertainty: Strategies for Facility Managers
For facility managers, staying informed is paramount. Regularly consulting trade and tariff updates can empower facility teams to anticipate changes effectively. Additionally, advocating for flexibility in project budgets to accommodate potential cost increases enables proactive management of expectations among stakeholders.
Conclusion: Be Prepared
The anticipated expansion of tariffs under the current administration creates an uncertain landscape for facility managers. Understanding which categories are most vulnerable, anticipating supply chain disruptions, and discovering opportunities for localized sourcing are crucial steps in navigating this complex issue. By preparing now and staying informed, facility managers can mitigate risks and set their projects up for success in an ever-evolving economic landscape.
Write A Comment